In our latest Circle Series spotlight, we talk to Nextgreen Founder and CEO Dato’ Lim Thiam Huat, whose quest to find solutions curbing the Malaysian palm oil industry’s environmental impact led to a revolutionary patented closed loop system technology integrating the Waste-to-Value concept.
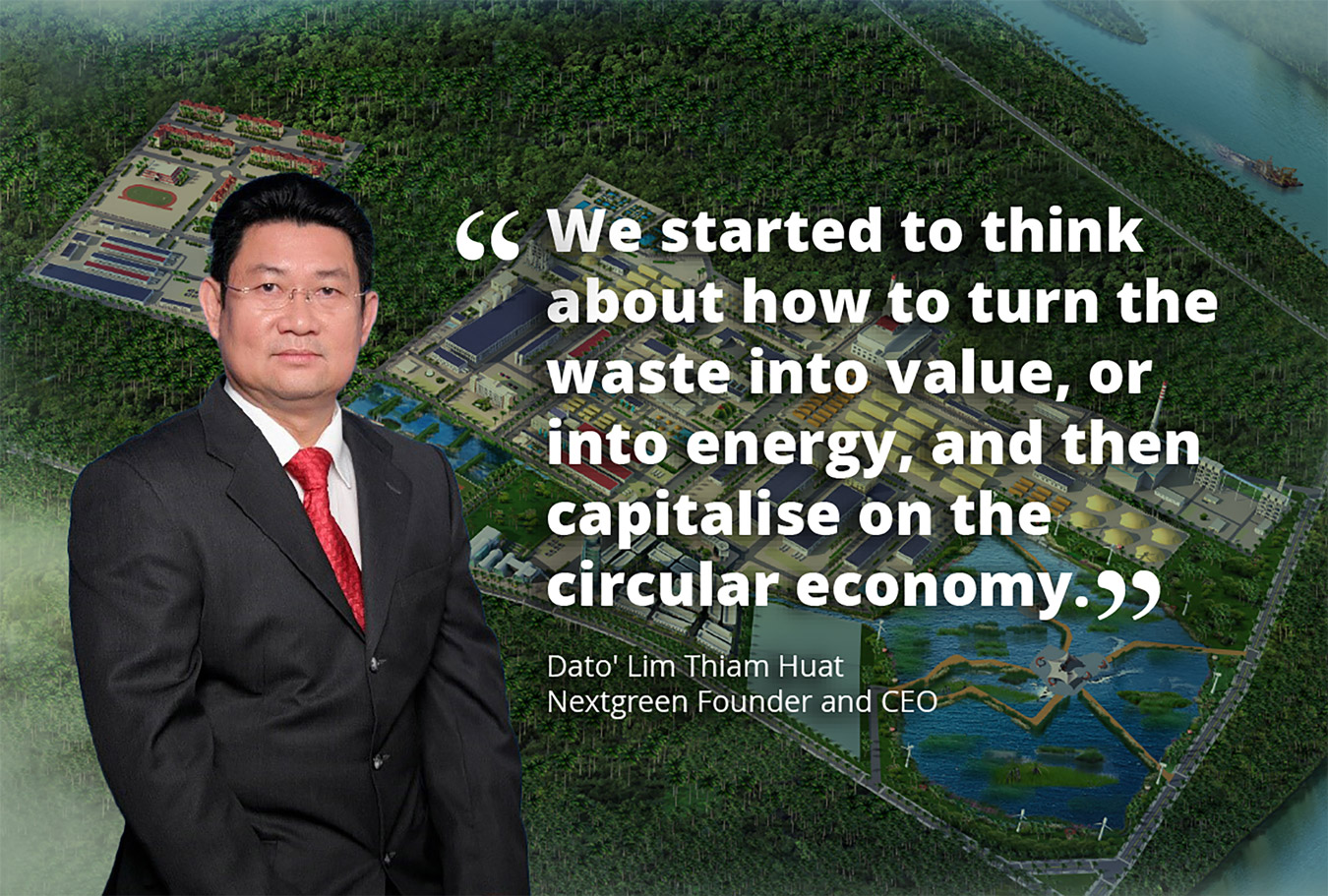
It’s an age-old proverb: “one man’s trash is another man’s treasure”. Or in this case, one industry’s waste is a company’s wealth.
Two decades ago, Nextgreen Founder and CEO Dato’ Lim Thiam Huat pondered on how to transform Malaysia’s abundant oil palm biomass into something of value, and significantly reduce the palm oil industry’s environmental impact. It was the seed that inspired his research on how to transform the palm oil industry’s voluminous Empty Fruit Bunches (EFB) to pulp, which eventually led to Nextgreen’s patented technology turning oil palm biomass into a diverse range of sustainable products.
Through a bio-integrated zero waste process, Nextgreen’s Green Technology Park (GTP) converts by-products of the palm oil production process into valuable material, including pulp and paper, fertilisers, animal feed and renewable energy. Today, the pioneering Nextgreen is at the forefront of the Green Economy, opening the doors for other commodities industries to tackle waste problems with similar innovative solutions.
What led to the creation of Nextgreen?
I started Nextgreen from the very beginning, 22 years ago. Before we went into this business, we were actually looking at the impact of the oil palm industry on the environment, and looking forward, what would be the best solution for the industry. I have a background of the construction industry and so I was also addressing the issue of how to convert either the by-products of the raw material we have, or the salvaged leftover raw material that can be reused. My learning curve started from there.
At that time, had the industry already been familiar with circular economy innovations?
At that point of time, not yet. I was looking for the best option or solution that could solve Malaysia’s oil palm industry problems. Being the second largest industry in Malaysia, it had a biomass issue. The challenge was the methodology of handling the biomass, and how to resolve the Empty Fruit Bunch (EFB) problem during that point of time.
What was the pioneering innovation of Nextgreen that addressed this problem?
The innovation was how we addressed the issue of waste in the palm oil industry, and resolved the entire problem by converting EFB into something else. We make sure there is no wastage, no other by-products or any other problematic issue to impact the environment. That’s when we started to think about how to turn the waste into value, or into energy, and then capitalise on the circular economy.
What was the first product line you began with?
We first started looking at pulp. We were looking at the EFB, which had a very high content of fibre, so we brought 5 kg of EFB from Malaysia to China to begin research and look for ways to go about its extraction.
The business solution we wanted to look at was upstream – how to actually get the waste from the biomass, convert into a valuable product, and become one of the sources of the raw material for the industry. That was one of the keys, and the reason why I was looking further with the research.
What were some of the major challenges you faced during this research phase?
I faced a lot of challenges in terms of technical aspects. For example, in the extraction of the EFB, we discovered a lot of black liquor from lignin (by-product of paper pulp production – Ed.) so we looked at how to resolve the issue using waste water treatments, and simultaneously identify the methodology that would be the best solution for the black liquor extraction, and convert it under the normal circumstances in the oil palm industry. Currently, the industry has no definitive solution; the options are to extract and burn it for energy, dump it, convert it into fertiliser, or use it to cover topsoil. These are different methodological approaches.
How has being an RSPO Member helped you along your journey to find sustainable solutions?
I believe it has set the direction in the market. RSPO provided clear indications of the requirements, and its criteria have helped strengthen our commitment to sustainability.For example, understanding the value chains and ensuring compliance with sustainable policies have become essential elements in the industry. These were the things that actually give us the indication to keep on going.
On the zero waste issue, I remember examining the Kyoto Protocol during the carbon credit era. At that time, RSPO was a key component for ensuring compliance across all value chains and downstream processes. However, we were never fully able to implement it. Even with RSPO Certification, the main advantage we gained was the ability to sell at a better price or premium. This scenario is typical in industries related to palm oil. Therefore, setting RSPO guidelines as a standard practice is crucial.
Your Green Technology Park is your flagship industrial complex. Could you walk us through its manufacturing operations?
The GTP sets in motion the Bio-Integrated Waste Concept. From the oil palm plantations, its FFB, goes into the palm oil mill, creating the Empty Fruit Bunches. From there, they go through the Grade 1, 2 and 3 and see the process.
It took me a lot of time to put together to achieve the Zero Waste concept with the integrations to fully capitalise making full use of the waste, into energy. An example of the process we do in my plant is when the raw materials coming from the EFB. We’ll be preprocessing the EFB by washing and pretreating it, then extracting the waste and residue oil contained in the EFB leftover by performing more pressing. The waste oil from the extraction process can be converted as an alternative feedstock and blended with any advanced biofuels such as Sustainable Aviation Fuels (SAF).
We then select the good fibre that would go to the pulp making. As for the leftover fibres and palm kernel shells – those are very high value products for energy, we can put them in our boiler to generate steam, and power for our production use. So this makes full use of the leftovers.
Those are short fibre and high content of the organic, we will actually move into our organic fertiliser plant.
Have other industries within or outside Malaysia approached you with this process? Would this Bio-Integrated concept be applicable to other industries?
Yes, I believe so, because this applies not only to oil palm. With other biomass, I believe there are also other methodologies that address this.
I’ve been approached by companies from Indonesia, Papua New Guinea and Africa. I think with commodity products, there’s no boundary, regardless of which country you are in, there is always an opportunity to leverage it and it depends on how much effort you undertake.
What’s next for Nextgreen?
I have a big mission to move forward with the Green Technology Park in Malaysia. I want to scale up our EFB Pulp mill to 100,000 MT. Subsequently, scale up to 200,000 and 400,000 MT. That becomes very economical and viable. We are also thinking about how to address the scaled up plants, as we’re looking at the environmental issues as well.
Based on your over two decades of experience with Nextgreen, what would you say is the business case for sustainability?
The big challenge is to integrate awareness of sustainability, the sustainability model, and the future direction of the business.
To set up the sustainability model, many factors were taken into our consideration. For example, when we started the collection centre, we had to maintain the efficient transportation of raw materials to our pulp mill at a lower cost, while also ensuring it had a low carbon footprint. Hence, the collection point has to be situated within the radius of 80 km of the mills, as anything beyond 80 km would incur a much higher cost of transportation while increasing the diesel usage, which would result in higher GHG emissions.
Subsequent to this, we also have to ensure the entire process benefits the palm oil mills for business continuity. With the selection of anchor tenants in the area, the palm oil mills will automatically receive tangible benefits when they contribute the raw materials. This will make the centres more productive and would be able to run self-sustainably.
At the same time, as an anchor contributing to the centre, it becomes viable. The residues are made into fertilisers that are sold, at a discounted rate, to the palm oil mills, which are able to distribute it to the plantations nearby with a low cost of transportation. This cultivates a true business partnership.
Keep reading

Open Letter to COP30 President: Integrating Forests and Biodiversity: A Policy Central to Paris Agreement Success
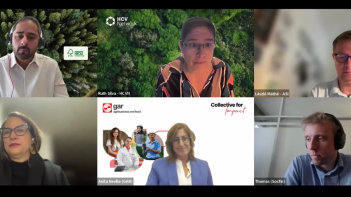
Bridging the Auditing Divide: Key Takeaways from the RSPO Assurance Forum 11
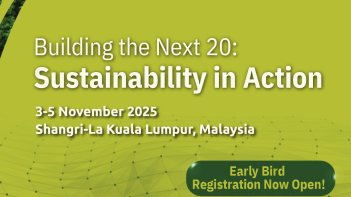
Good News: RT2025 Early Bird Registration Extended!
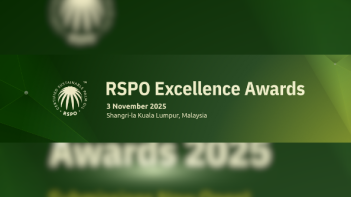
Extension of RSPO Excellence Awards 2025 Submission Deadline!
Call for Expression of Interest: Ghana National Interpretation Task Force for 2024 RSPO Principles and Criteria (RSPO P&C)
Call for Expression of Interest: Côte D’Ivoire National Interpretation Task Force for 2024 RSPO Principles and Criteria (RSPO P&C) and Independent Smallholder (ISH) Standard
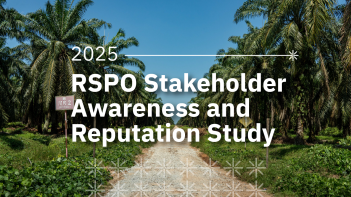
RSPO Gains Global Recognition in 2025 Stakeholder Study
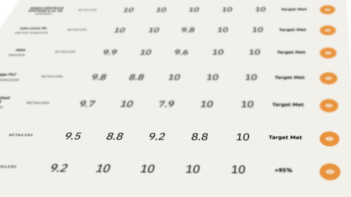
Top 9 Retailers In Europe Committing To Sustainable Palm Oil
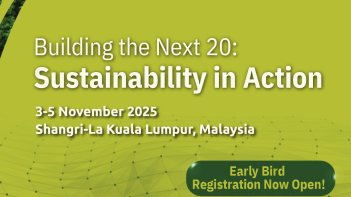